Perfil

The step beam plays a vital role in heavy-duty pallet racking systems, directly influencing the strength and load-bearing capacity of the entire structure.
Manufacturers typically utilize roll forming machines with 1.5-2mm hot-rolled or cold-rolled steel to produce step beams. To enhance their lifespan and prevent deformation caused by steel coil tension, welding is applied at the steel coil joints. Two common welding processes employed in the industry are MIG welder (as in this case) and laser full welder.
Both MIG welder and laser full welder contribute to reinforcing structural integrity. However, due to the comprehensive coverage of joints in full welding, its effectiveness surpasses that of MIG welding. Customers can select the welding method based on their budget and rack loading requirements.
Real case-Main Techinical Parameters
Flow chart

Manual decoiler--Guiding--Leveler--Roll forming machine--Flying welder--Flying saw cutting--Out table
Main Techinical Parameters
1.Line speed: 4-5 m/min, adjustable
2.Profiles: Multiple sizes-same width of 66mm,and different height of 76.2-165.1mm
3.Material thickness: 1.9mm (in this case)
4.Suitable material:Hot rolled steel, cold rolled steel, galvanized steel
5.Roll forming machine: Cast-iron structureand chain driving system.
6.No. Of forming station: 26
7.Welding system: 2*welding torches, roll former doesn’t stop when welding.
8.Cutting system: Saw cutting, rollformer doesn’t stop when cutting.
9.Changing size: Automatically.
10.PLC cabinet: Siemens system.

Real case-Description
Manual Decoiler
The manual decoiler features a brake device designed to adjust core expansion tension within the range of φ490-510 mm, ensuring smooth uncoiling operations. Given the use of a 1.9mm steel coil, there is a risk of sudden popping open during uncoiling. To address this safety concern, a press arm is installed to securely hold the steel coil in place, while protective steel blades are added to prevent coil slippage. This design not only offers a cost-effective solution but also prioritizes safety in the uncoiling process.
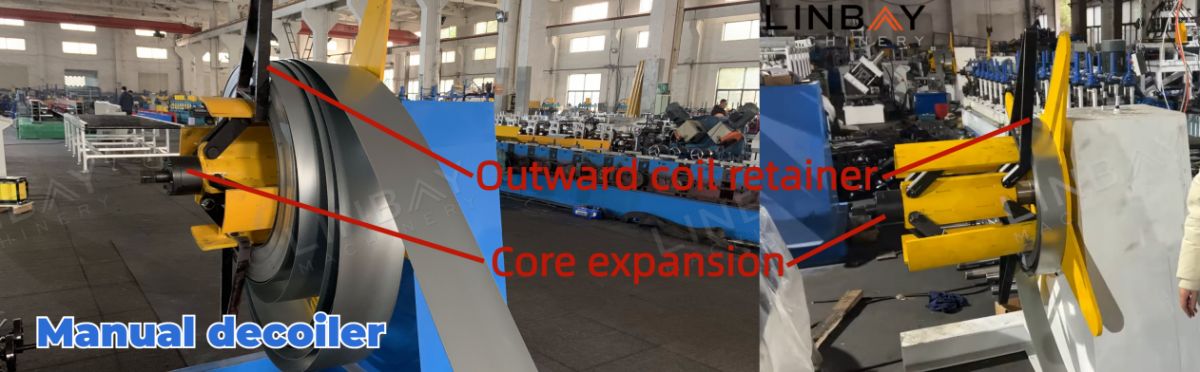
The manual decoiler has no power. For higher production capacity requirements, we provide an optional hydraulic decoiler powered by a hydraulic station.
Guiding & Digital display
Guiding rollers play a crucial role in maintaining alignment between the steel coil and the machines, thereby preventing distortion of the step beam and participating in the roll forming process to prevent rebound deformation of the steel. The straightness of the step beam is pivotal for product quality and impacts the load-bearing performance of the entire racking system. Guiding rollers are strategically positioned not only at the outset of the roll forming machine but also at various points along the entire roll forming line, ensuring precise alignment throughout the production process.
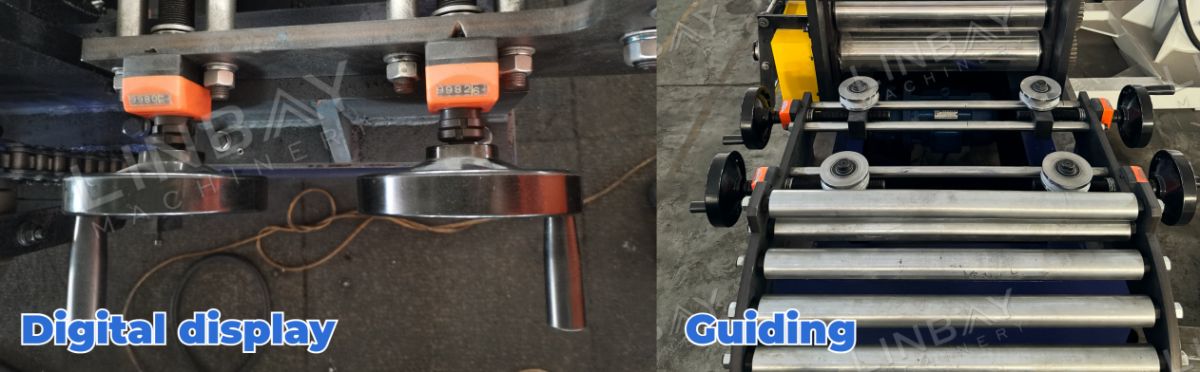
Digital display devices facilitate the convenient recording of the correct position of the guiding rollers. And measurements of the distance from each guiding roller to the left and right edges of the roll forming machine are recorded in the manual, allowing for easy adjustments based on these data even if slight displacements occur during transportation or production.
Leveler
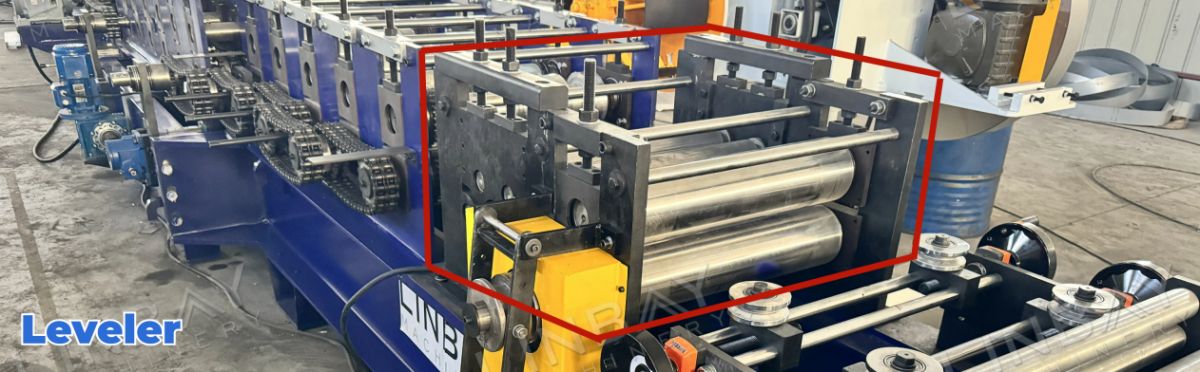
Following this, the steel coil proceeds into the leveler. Given its thickness of 1.9mm, it is imperative to eliminate any curvature present in the steel coil, thereby improving its flatness and parallelism for the quality of the step beam. Equipped with 3 upper and 4 lower leveling rollers, the leveler efficiently achieves this objective, ensuring optimal flatness and parallelism for the subsequent roll forming process.
Roll Forming Machine
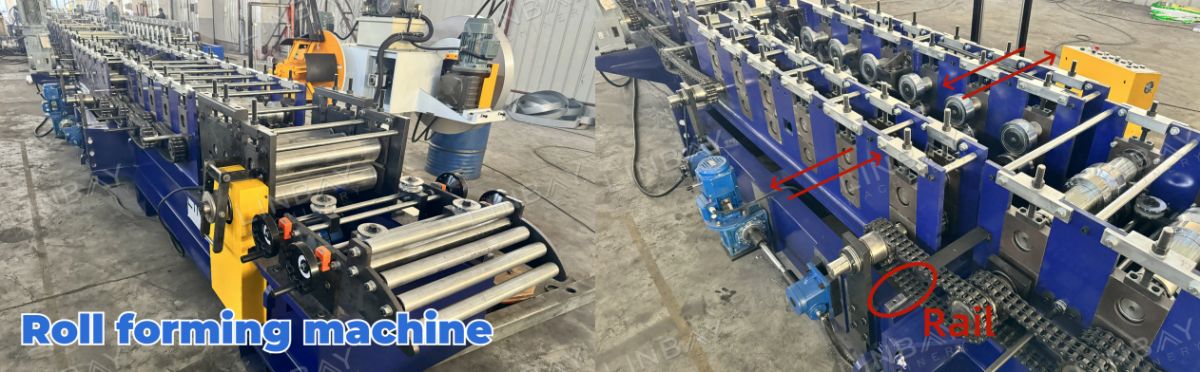
At the heart of the entire production line lies the roll forming machine. Equipped with variable speed control facilitated by a (Japanese brand) Yaskawa inverter, the machine offers a versatile speed range from 0 to 10m/min, ensuring adaptability to diverse production requirements. Featuring 26 forming stations, it utilizes a wall-panel structure and chain-driving system, meticulously engineered to deliver precision and efficiency in the forming process. With its cutting-edge technology and robust design, the roll forming machine serves as the cornerstone of quality and productivity within the production line.
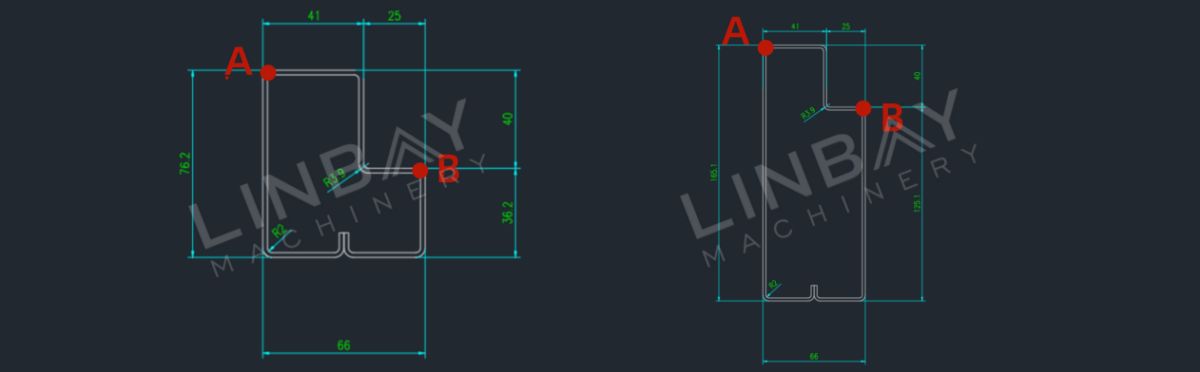
Capable of producing various sizes, with a width of 66mm and a height ranging from 76.2 to 165.1mm, this system offers flexibility in output. Upon inputting the desired bottom width and height into the PLC control cabinet, the forming stations automatically adjust to precise positions and modify key forming points (A and B points), facilitating size changes in approximately 10 minutes. Height adjustments correspond to variations in key forming points (A and B points), enabling the production of step beams with different heights.
Gcr15, a high-carbon chromium-bearing steel renowned for its hardness and wear resistance, is utilized for the material of forming rollers. To extend durability, the rollers undergo chrome plating. Additionally, shafts made of 40Cr material undergo heat treatment, enhancing strength and ensuring robust construction.
Flying MIG Welder
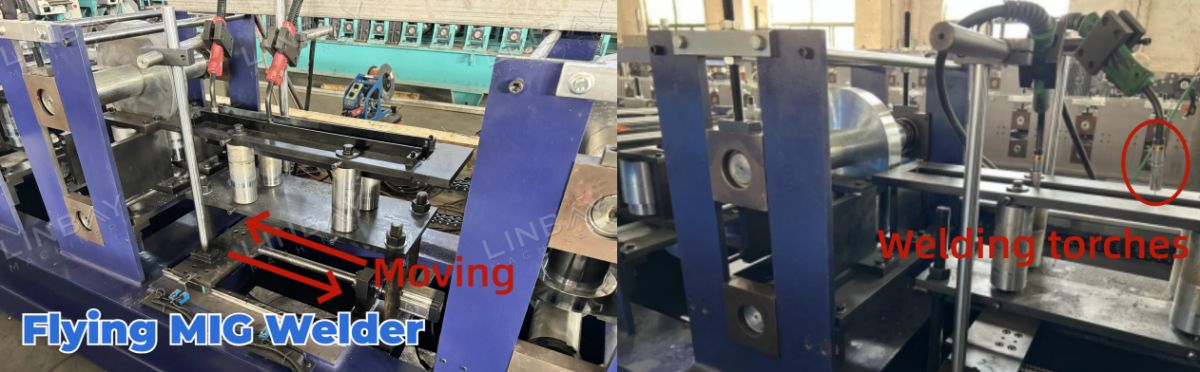
To prolong the lifespan of the step beam and prevent separation at the steel coil joints, welding is employed at the joints of steel coils in a dot pattern. The spacing between each dot is adjustable according to customer requirements. Additionally, two welding torches are installed to increase line speed. These torches can move simultaneously with the roll forming speed, ensuring continuous operation of the roll forming machine.
Flying Saw Cutting
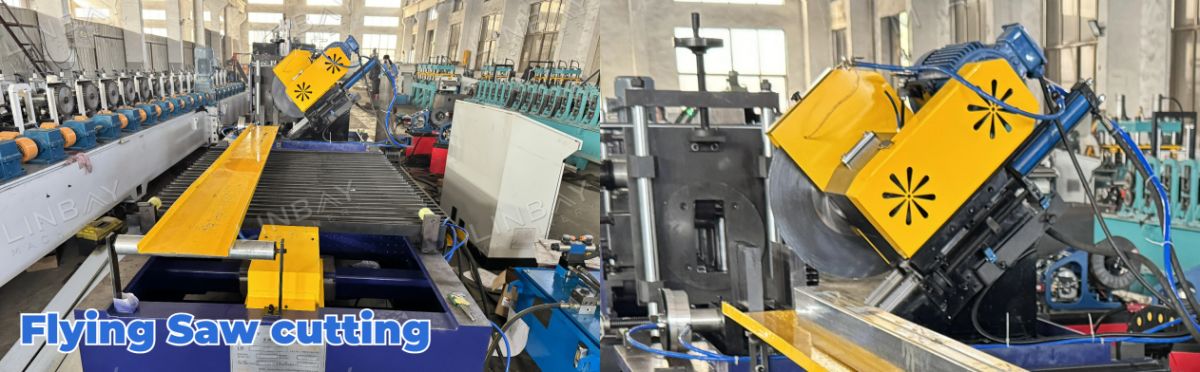
Following roll forming, the step beam advances to the cutting machine, employing a saw cutting machine due to the closed shape of the step beam. Specialized saw blades guarantee high precision and hardness, while a cooling sprayer safeguards the saw blades, extending their lifespan. Although the saw cutting speed is slower than hydraulic shearing, a mobile function is incorporated to synchronize with the roll forming machine's production speed, ensuring uninterrupted operation. Moreover, the saw cutting machine ensures minimal waste during steel coil replacement and profile cutting.
Encoder & PLC
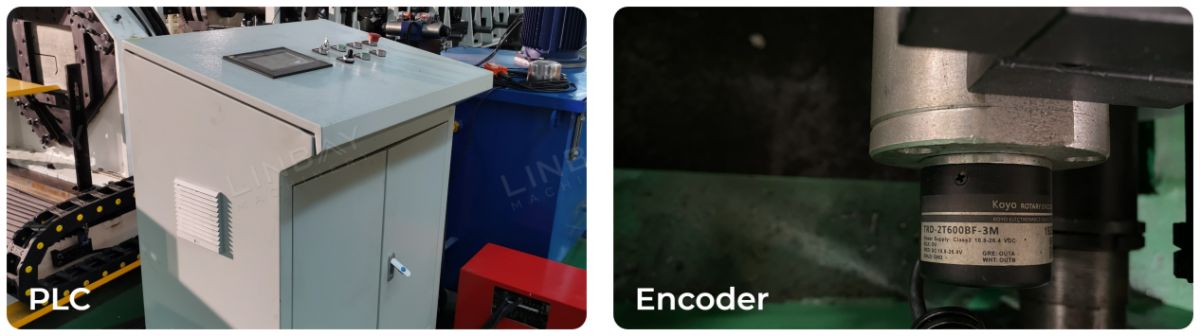
Within the roll forming machine, a Japanese Koyo encoder accurately converts the sensed coil length into an electrical signal, which is then transmitted to the PLC control cabinet. A motion controller, housed within the electrical control cabinet, ensures seamless acceleration and deceleration during the forward and backward movement of the cutting machine, thereby achieving precise cutting length accuracy. This meticulous control mechanism guarantees stable and smooth welding marks, preventing step beams from cracking and ensuring stable, high-quality production. Operators can easily manage production speed, set production dimensions, cutting length, and more through the PLC screen. Furthermore, the PLC control cabinet features a memory storage function for commonly used parameters and provides protection against overload, short circuit, and phase loss, ensuring operational reliability and safety.
The language on the PLC screen can be customized according to the customers' requirements.
Hydraulic Station
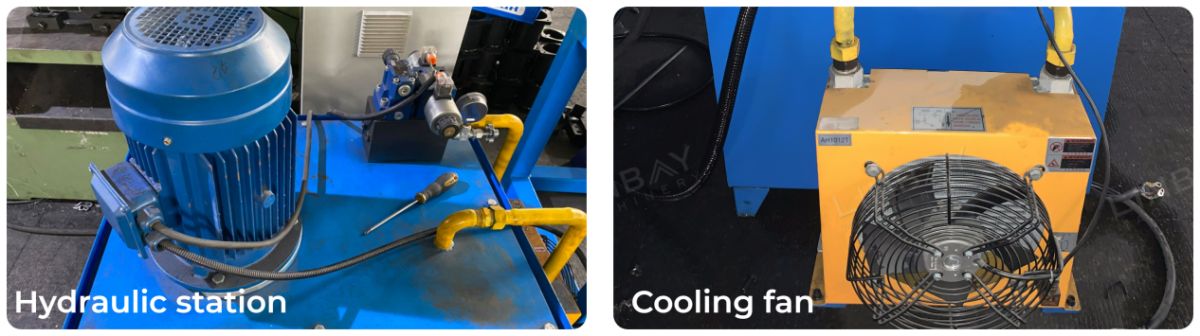
Our hydraulic station features a cooling electric fan to efficiently dissipate heat, ensuring prolonged and reliable operation with low failure rates.
Warranty
Upon shipment, the delivery date is indicated on the steel nameplate, providing a two-year guarantee for the entire production line and a five-year warranty for rollers and shafts.
1. Decoiler
2. Feeding
3.Punching
4. Roll forming stands
5. Driving system
6. Cutting system
Others
Out table