video
Profile
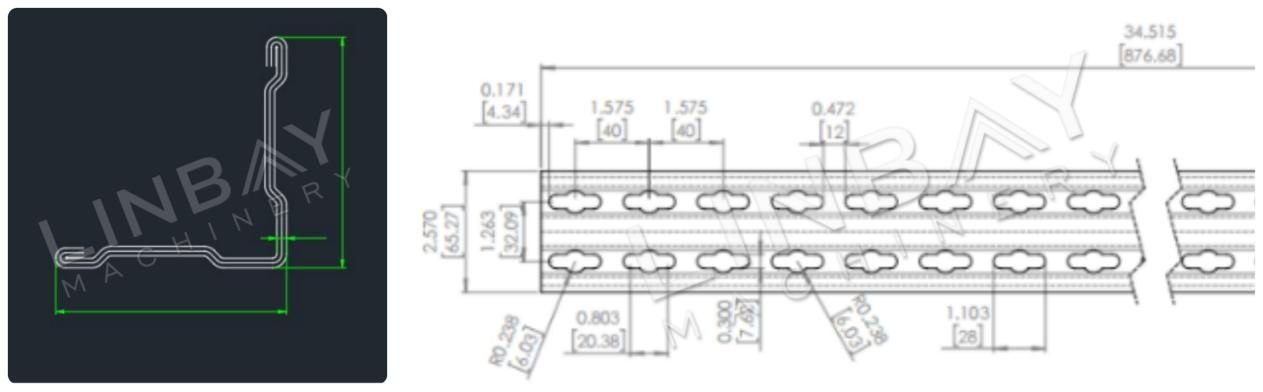
This is a light-duty shelf upright, resembling angle steel, with a thickness of 1.2mm. It is a key component of the shelf structure, and its straightness directly affects the load-bearing capacity of the shelf. Holes are punched on both sides to connect the beams.
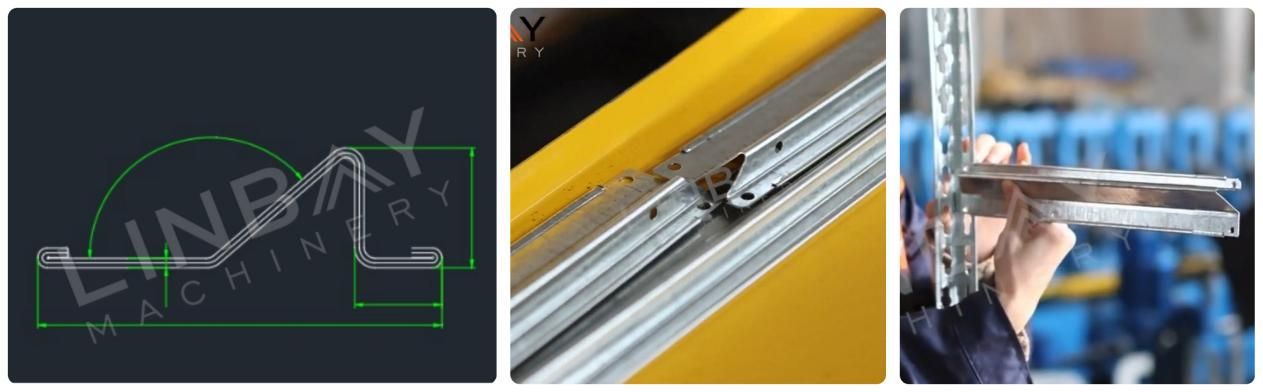
This is a light-duty shelf beam, 1.2mm thick, intended to support shelf panels and improve the overall load-bearing capacity of the light-duty shelf.
Description
Flow chart

Decoiler with Leveler
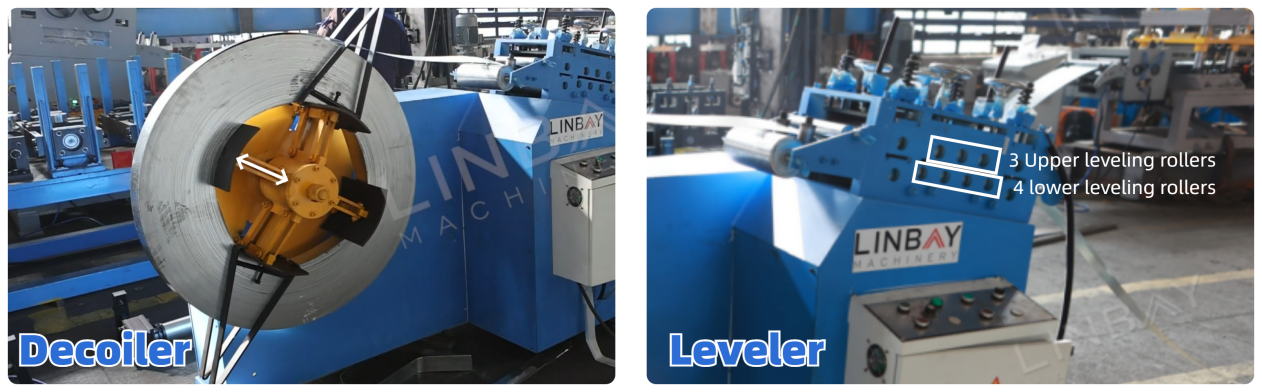
This machine combines decoiling and leveling functionalities. It includes a brake device on the decoiler for adjusting decoiling roller tension, ensuring smooth speed. Protective steel leaves prevent coil slipping. This design offers a cost-effective, high-security decoiling solution.
Afterward, the steel coil enters the leveling machine. At 1.2mm thick, dense punching requires leveling to eliminate coil curvature, enhancing flatness and parallelism for improved product quality. The leveler has 3 upper and 4 lower rollers.
Servo Feeder & Hydraulic Punch
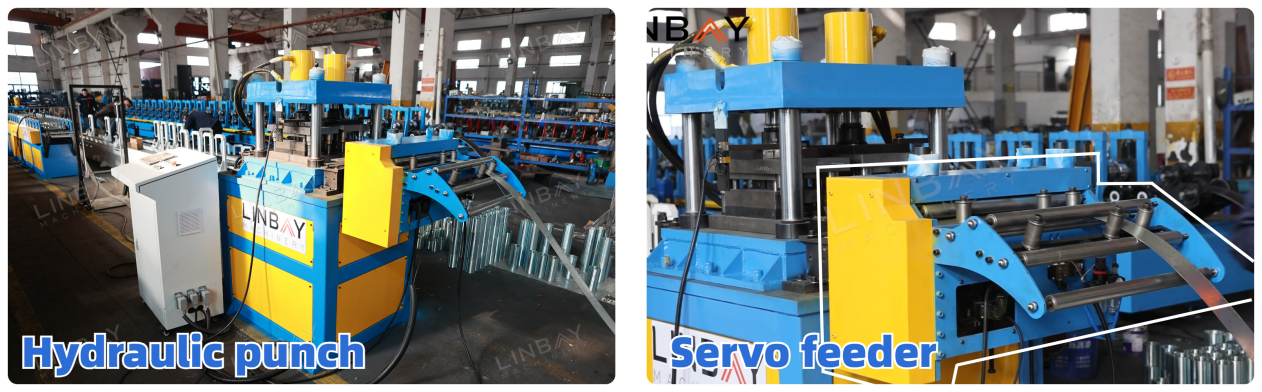
The steel coil proceeds to an independent hydraulic punch machine. Utilizing a servo motor for the feeder enables precise punching due to its rapid response and minimal start-stop time, ensuring accurate punching position control.
Limiter
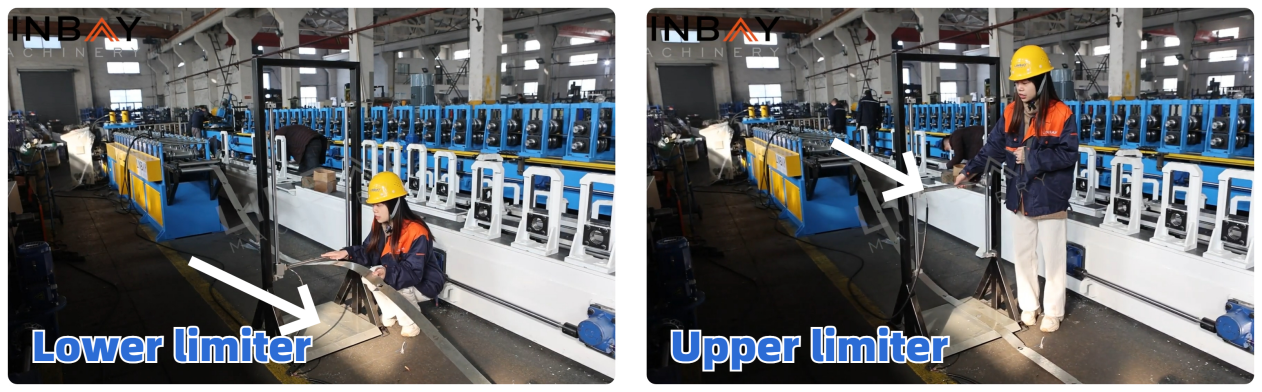
During the punching and roll forming processes, a limiter is employed to synchronize production speed. When the steel coil reaches the lower limiter, indicating a higher punching speed than roll forming speed, the hydraulic punch receives a stop signal from the PLC control cabinet. A prompt alarm displays on the PLC screen, allowing the operator to resume work with a screen click. Meanwhile, during the pause, the roll forming machine continues operating.
Conversely, when the steel coil hits the upper limiter, indicating higher forming speed than punching speed, the roll forming machine halts. During the brief pause between the roll forming machine stopping and restarting, the hydraulic punch remains operational. The height of the upper limiter is adjustable based on customer requirements.
This ensures overall coordination and uniform production speed of the production line.
Guiding
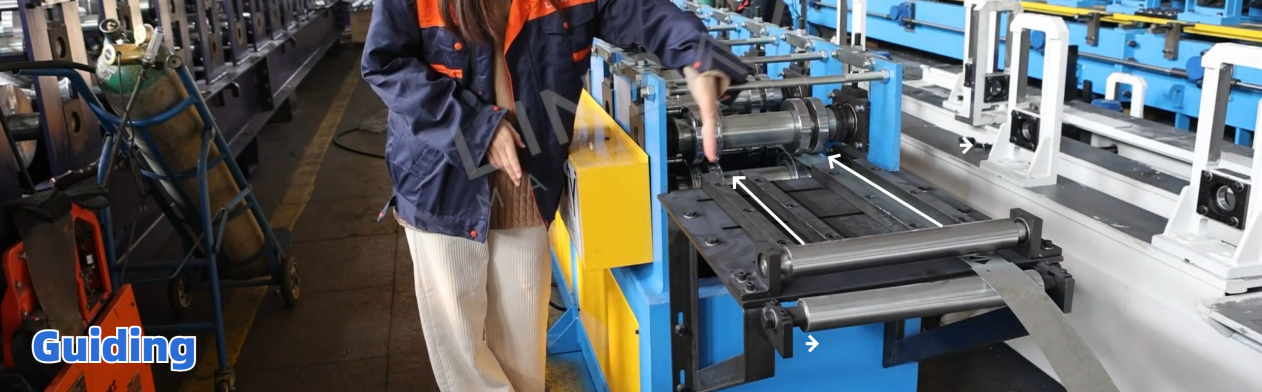
Before the steel coil enters the initial forming roller, it traverses a guiding bar to maintain alignment with the machine, preventing profile distortion. Guiding rollers are strategically positioned not only at the entry but also along the entire forming line. Measurements of each guiding bar/roller's distance to the edge are documented in the manual for precise adjustment in case of displacement during transport or worker-induced misalignment during production.
Roll Forming Machine
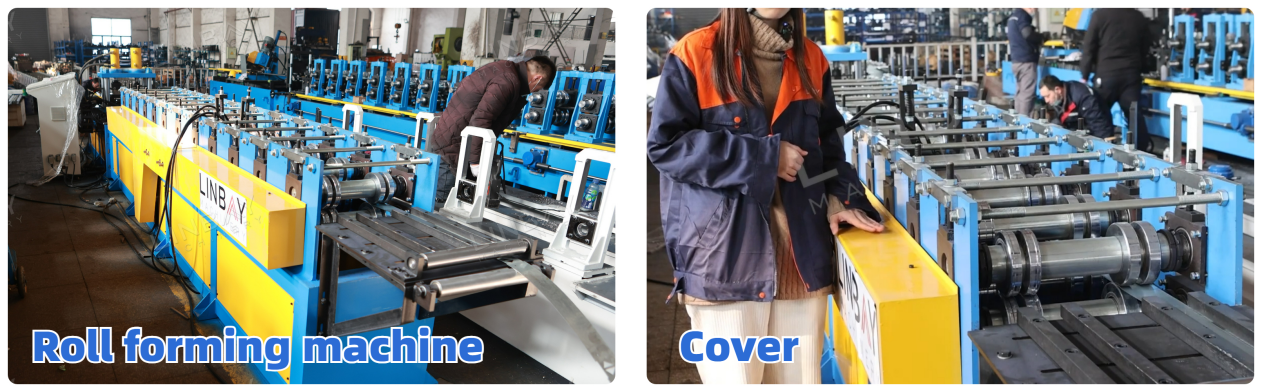
The roll forming machine stands as the pivotal component of the entire production line. With 12 forming stations, it boasts a wall panel structure and chain driving system. Notably, it's a double-row design capable of crafting both upright and beam shapes for light-duty shelving. While these rows can't operate simultaneously, they provide flexibility for diverse production demands. Protective covers on the chain prioritize worker safety. Additionally, the machine undergoes testing with steel coils of equivalent yield strength to those used in customer production, ensuring immediate convenience upon delivery.
The forming rollers are crafted from Gcr15, a high-carbon chromium bearing steel renowned for its hardness and wear resistance. Chrome plating on the roller surface prolongs its lifespan, while the shafts are composed of heat-treated 40Cr material.
Flying Hydraulic Cutting & Encoder
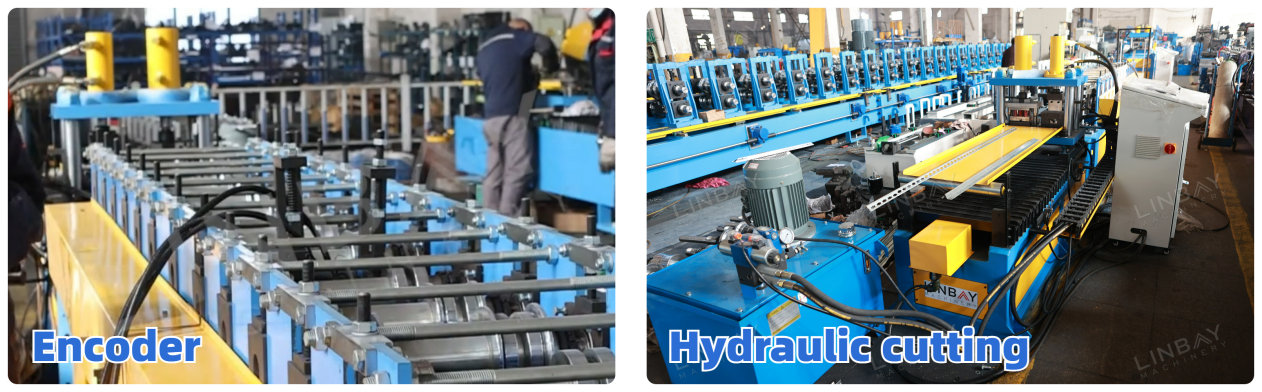
The roll forming machine integrates a Japanese Koyo encoder, converting sensed steel coil length into electrical signals sent to the PLC control cabinet. This enables the cutting machine to control cutting errors within 1mm, ensuring high-quality products and reducing waste from incorrect cuts. "Flying" denotes the cutting machine's capability to move back and forth at the same speed as the roll forming machine during cutting, enabling continuous operation and enhancing overall production line capacity.
Hydraulic Station
The hydraulic station is equipped with a cooling electric fan for efficient heat dissipation, ensuring prolonged, low-fault operation, and durability.
PLC
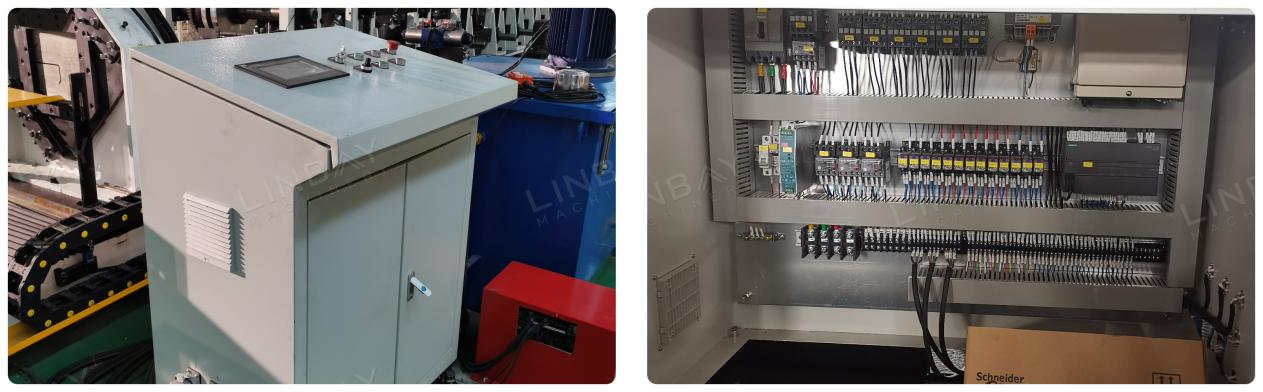
Workers can manage production speed, set production dimensions, cutting lengths, etc., via the PLC screen. The PLC control cabinet incorporates protective functions like overload, short circuit, and phase loss protection. The language displayed on the PLC screen can be customized to a single language or multiple languages based on customer requirements.
Warranty
Before delivery, the delivery date is indicated on the nameplate, starting a two-year guarantee for the entire production line and a five-year warranty for rollers and shafts.
1. Decoiler
2. Feeding
3.Punching
4. Roll forming stands
5. Driving system
6. Cutting system
Others
Out table