video
Profile
Decoiler--Roll former--Hydraulic cut--Out table
7.5 Ton Hydraulic Decoiler
For this production line, we employ a hydraulic decoiler capable of handling loads up to 7.5 tons. Given the necessity for wide steel coils in manufacturing trapezoidal panels, the coil changing process presents potential safety hazards for workers. To mitigate these risks, protective iron leaves are installed on the outer side of the coil to prevent slipping during decoiling, emphasizing the importance of worker safety in our design considerations.
An optional loading car is available, aiding in the transportation of coils to the decoiler. This device helps save time and improves worker safety, particularly in facilities lacking overhead cranes.
Roll Forming Machine
The roll forming machine serves as the pivotal component in this production line, boasting 20 forming stations in total. It utilizes a wall panel structure and a chain driving system. The forming rollers, crafted from Gcr15, a high-carbon chromium-bearing steel, offer exceptional hardness and wear resistance. Chrome plating on the roller surface extends its lifespan, while the shafts are constructed from heat-treated 40Cr material.
Protective covers on the chain serve to prevent dust buildup or fragments from damaging the chains, thus ensuring worker safety. The roll forming machine undergoes testing using steel coils with the same yield strength as those used in customer production, facilitating convenient production upon delivery.
Hydraulic Cut & Encoder
The roll forming machine integrates a Koyo encoder sourced from Japan, which converts sensed steel coil length into electrical signals transmitted to the PLC control cabinet. This precise system enables the cutting machine to maintain cutting errors within a tolerance of 1mm, ensuring high product quality and minimizing waste from incorrect cuts. Powered by the hydraulic station, the hydraulic cutting machine delivers robust cutting force. Its cutting process generates no waste, leaving smooth edges without burrs. We meticulously test the roll forming machine until it produces a profile that matches the drawing, after which we manufacture blade molds based on the sample. While this approach may marginally increase time and labor costs, the resulting cutting machine exhibits exceptionally smooth edges without any burrs.
Hydraulic Station
Equipped with cooling electric fans, our hydraulic station ensures efficient heat dissipation, allowing for continuous and cool operation, thereby enhancing work efficiency. With a low failure rate and long-term durability, our hydraulic station is reliable and built to last.
PLC control cabinet
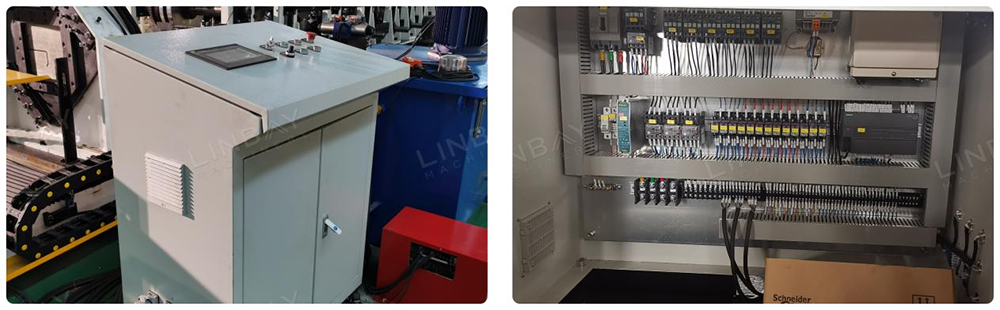
Workers have the ability to control production speed, adjust production dimensions, cutting lengths, and more via the PLC screen. The PLC control cabinet is equipped with protective functions including overload, short circuit, and phase loss protection. Additionally, the language displayed on the PLC screen can be customized to meet specific customer requirements, accommodating single or multiple languages as needed.
Regular Out Table & Optional: Auto Stacker
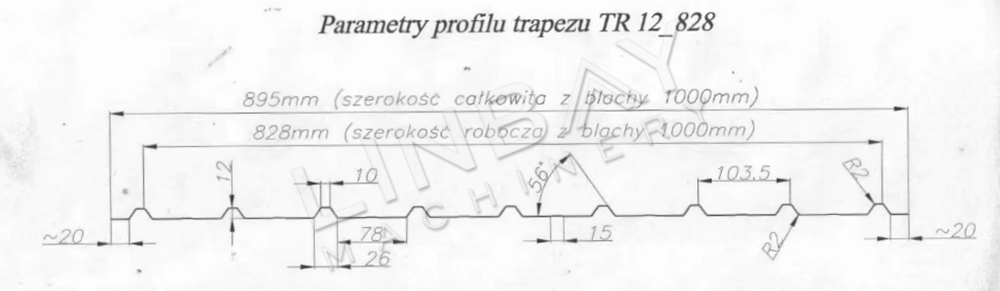
This trapezoidal panel is a standard roofing and cladding material widely utilized in Romania across various applications such as industrial and construction projects, small warehouses, sheds, and agricultural facilities.
Manufactured through a cold roll forming process, this panel boasts an overall width of 895mm, a cover width of 828mm, and features a 12mm wave height, with upper and lower wave widths of 10mm and 26mm respectively. The wave pitch measures 78mm. It is available in thicknesses ranging from 0.3mm to 0.6mm and can be produced using galvanized steel, aluminum steel, or color-coated steel coils. Galvalume steel is particularly favored for its superior anti-rust properties compared to galvanized steel.
Description
Flow chart
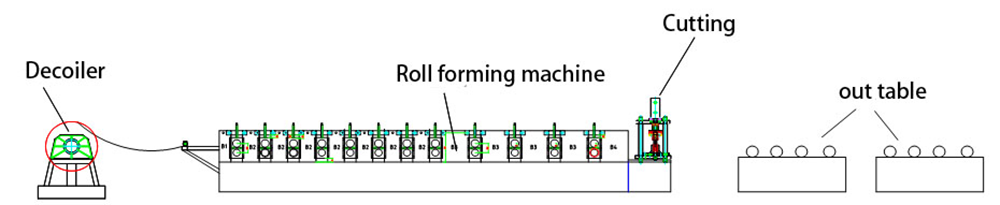
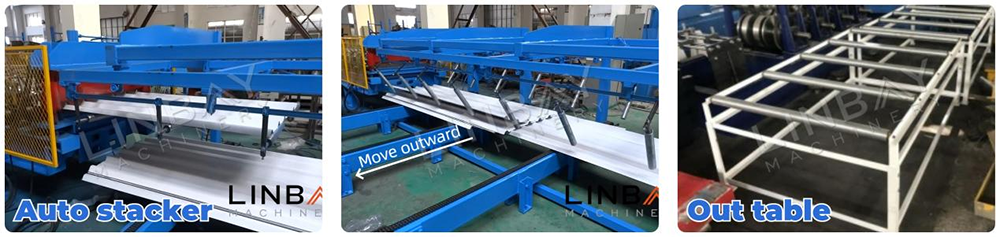
A standard out table is provided for transporting productions, offering a non-powered solution that can be customized in length and width to meet the specific requirements of customers.
For trapezoidal panels exceeding 6 meters in length, we suggest utilizing an auto stacker to minimize manual labor costs and improve efficiency and work safety. Following cutting, the trapezoidal panels are conveyed to the stacker's swing arm, where they are carefully layered. Subsequently, the panels are transported outward along the conveyor.
Other optional: Ink printer
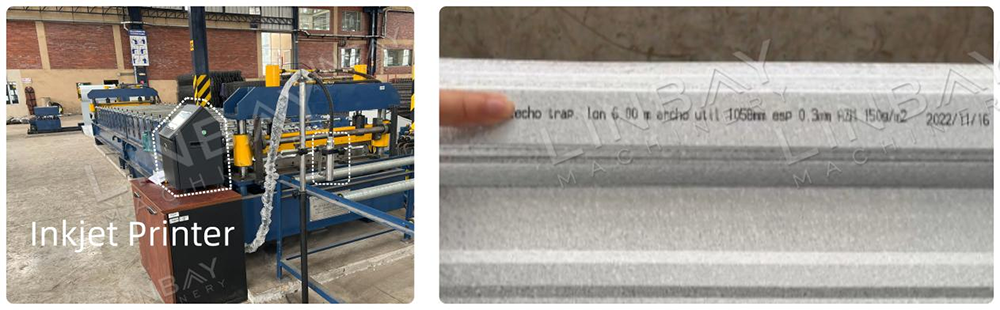
Customers have the option to utilize an ink printer to print company names, logos, profile numbers, and other pertinent information onto the surface of the panels. This facilitates rapid market expansion and increased visibility for companies. The ink dries rapidly and does not pose a risk of contaminating the surface.
Warranty
Before delivery, the delivery date is indicated on the nameplate, starting a two-year guarantee for the entire production line and a five-year warranty for rollers and shafts.
1. Decoiler
2. Feeding
3.Punching
4. Roll forming stands
5. Driving system
6. Cutting system
Others
Out table