Profile
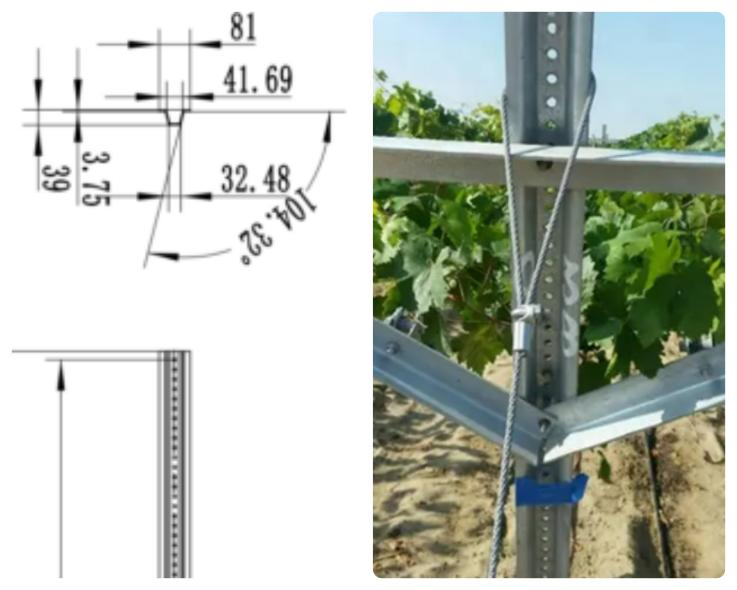
The Trellis U-channel post is a hat-shaped fence post commonly used in the agricultural sector, particularly for grape trellises, apple frames, and similar applications. It features a top width of 32.48mm, a bottom width of 41.69mm, and a total width of 81mm, with a height of 39mm. Each post measures 2473.2mm in length and is equipped with 107 closely spaced, continuous 9mm diameter holes, allowing for flexible installation of brackets in various sizes.
Description
Flow chart
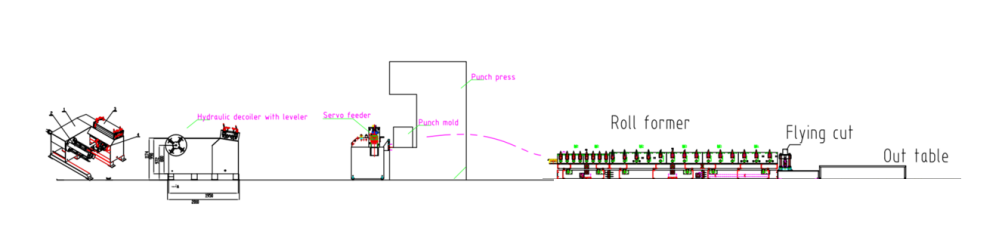
Decoiler with leveler--Servo feeder--Punch press--Roll former--Flying cut--Out table
Decoiler with Leveler
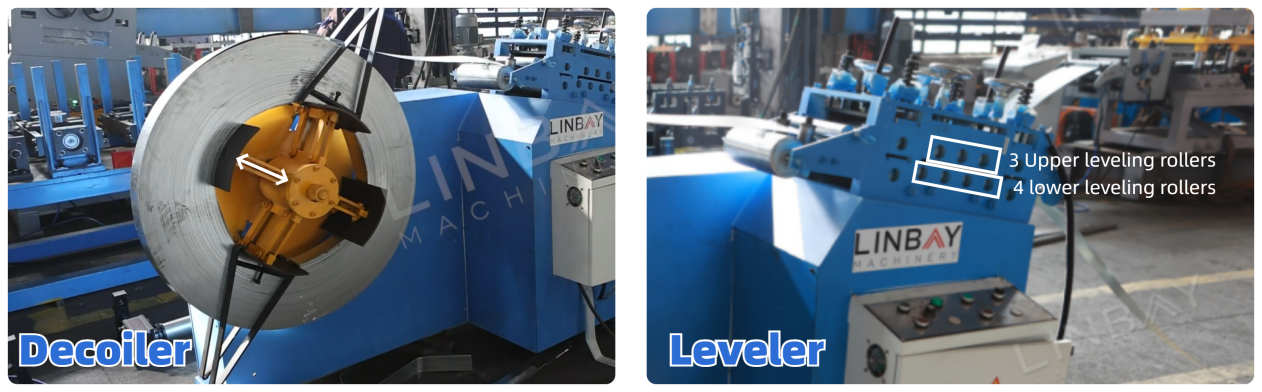
This machine combines decoiling and leveling functionalities. Its decoiler features a brake device for adjusting the tension of the decoiling roller, ensuring smooth operation. Steel protection leaves prevent coil slippage during decoiling, enhancing safety and cost-effectiveness while saving production line floor space.
Following decoiling, the steel coil proceeds to the leveling machine. Given the coil thickness (2.7-3.2mm) and dense punching, a leveler is crucial to eliminating coil curvature, enhancing flatness and parallelism. The leveling machine is equipped with 3 upper and 4 lower leveling rollers for optimal performance.
Servo Feeder & Punch Press
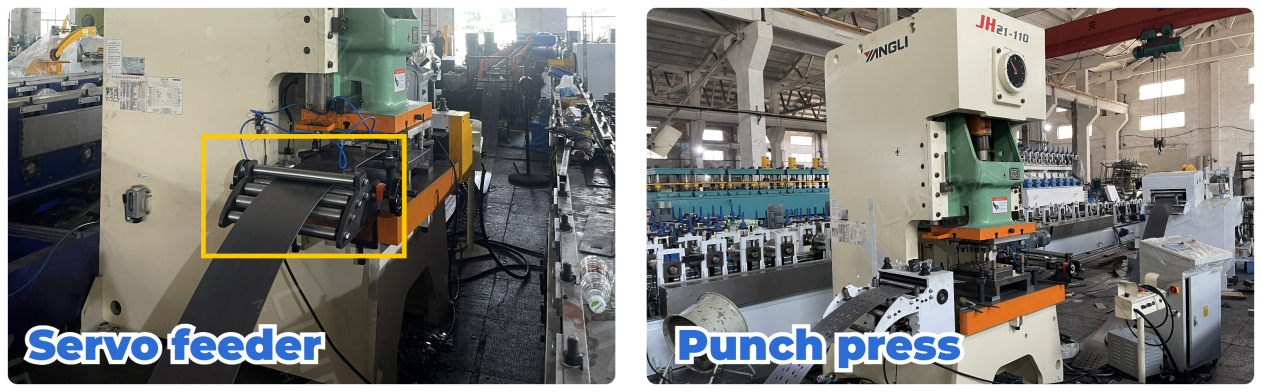
For this purpose, we employ a 110-ton punching press manufactured by the Yangli brand, coupled with a servo feeder. The servo motor enables rapid response with minimal start-stop time wastage, ensuring precise position control. With Yangli's global presence and commitment to high-quality after-sales service, customers can expect reliable support. Customized molds are tailored based on customer-provided punching drawings, efficiently creating 9mm diameter holes. The punching dies, constructed from SKD-11 steel, offer exceptional wear resistance and hardness.
In the PLC control program, we streamline the input of punching data by managing the quantity of punching holes. Additionally, a parameter memory function is provided for storing 10 sets of punching parameters, tailored to production requirements. This feature allows for easy retrieval and use of stored parameters without the need for re-input.
Limiter
To synchronize production speed, a limiter is positioned between the punching and roll forming sections. When the steel coil contacts the lower limiter, signaling a punching speed surpassing the roll forming speed, the punching machine receives a stop signal. A prompt appears on the PLC screen, prompting the operator to resume work by clicking on the screen.
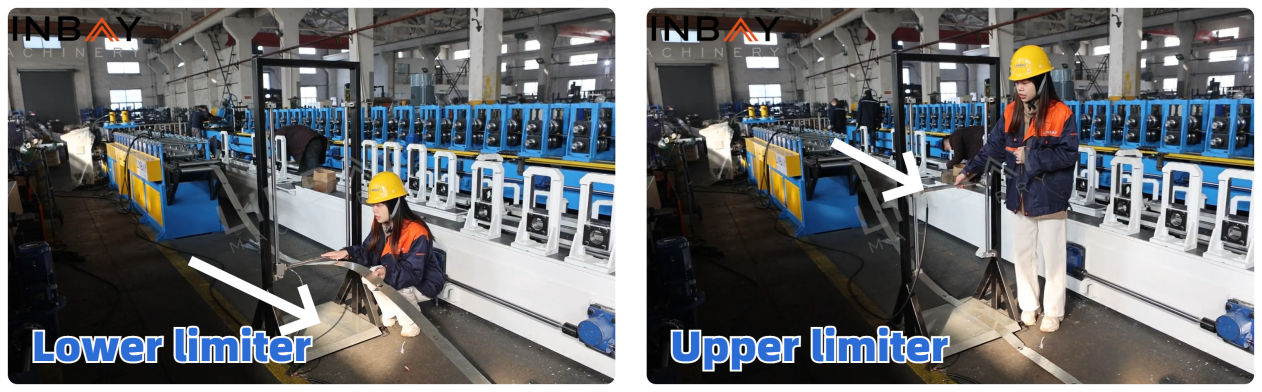
On the contrary, if the steel coil touches the upper limiter, suggesting a roll forming speed exceeding the punching speed, the roll forming machine halts operation. While the roll forming machine resumes work, the punching machine continues its operation without interruption.
This setup ensures overall coordination and uniformity of production speed on the production line.
Guiding
Prior to entering the initial set of forming rollers, the steel coil is directed through a guide section using guiding rollers. These rollers ensure alignment between the coil and the machine's centerline, preventing distortion of formed profiles. Guiding rollers are strategically positioned along the entire forming line. Measurements from each guiding roller to the edge are documented in the manual, facilitating effortless repositioning if slight displacement occurs during transportation or production adjustments.
Roll Forming Machine
At the heart of the production line lies the roll forming machine, a pivotal component comprising 10 forming stations. It boasts a sturdy cast-iron structure and a gearbox driving system, achieving a formidable forming speed of up to 15m/min. Crafted from Cr12 high-carbon chromium-bearing steel, the forming rollers excel in hardness and wear resistance. To prolong their lifespan, the rollers undergo chrome plating, while the shafts are constructed from 40Cr material.
Flying Laser Coder (Optional)
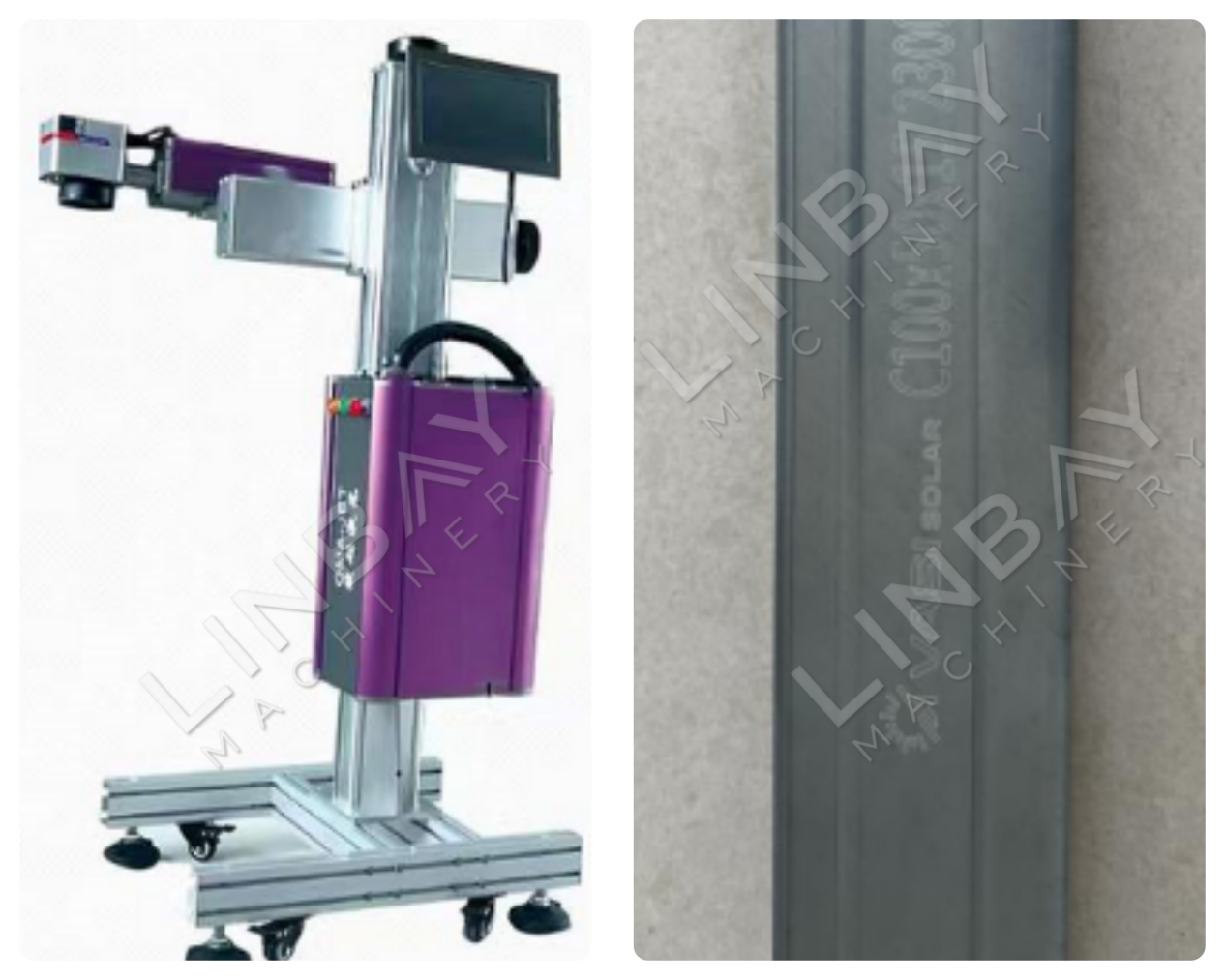
Prior to the cutting process, an optional laser coder can be installed, synchronized with the cutting machine's speed without interrupting the continuous operation of the roll forming machine. This advanced system is equipped with a touchscreen interface, induction eyes, and a lifting bracket. It facilitates laser printing of various elements such as text, graphics, QR codes, and more. This automation aids in standardizing products, controlling production, and promoting the brand effectively.
Flying Hydraulic Cutting & Encoder
Inside the forming machine, a Koyo encoder from Japan transforms the detected length of the steel coil into an electrical signal, which is then transmitted to the PLC control cabinet. This allows for precise control of cutting errors, ensuring product quality within a 1mm margin and reducing waste. The cutting molds are specifically designed to match the profile, ensuring smooth, burr-free cuts without any deformation. The term "flying" indicates that the cutting machine can move at the same speed as the roll forming process, enabling seamless operation and boosting overall production efficiency.
Hydraulic Station
The hydraulic station is equipped with integrated cooling fans to effectively dissipate heat, ensuring continuous operation and longevity. Known for its low failure rate, the hydraulic station is engineered for extended durability.
PLC control cabinet
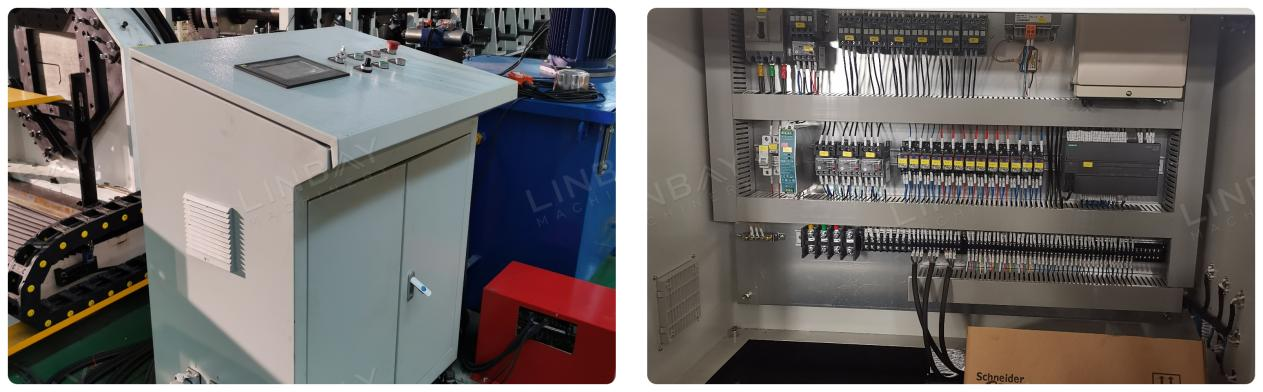
Through the PLC screen, operators have the capability to manage production speed, define production dimensions, cutting lengths, and more. Safety features incorporated into the PLC control cabinet encompass protection against overload, short circuit, and phase loss. Furthermore, the language displayed on the PLC screen can be tailored to align with customer preferences.
Warranty
The production line is provided with a two-year warranty from the delivery date, indicated on the nameplate. The rollers and shafts receive a five-year warranty.
1. Decoiler
2. Feeding
3.Punching
4. Roll forming stands
5. Driving system
6. Cutting system
Others
Out table