VIDEO
Perfil
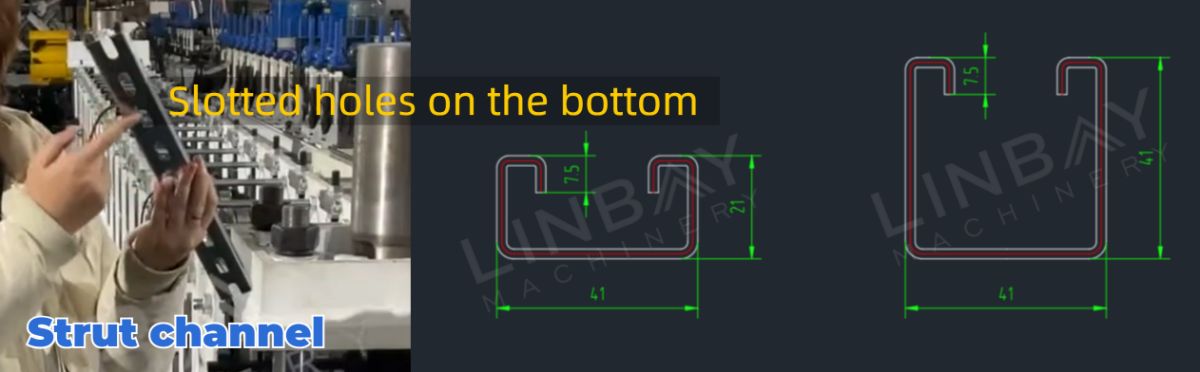
Strut channel serves as a vital component for supporting and connecting lightweight structural loads in building construction. Standard dimensions for strut channels often include 41*21mm and 41*41mm. These channels are commonly crafted from materials such as hot-rolled steel, cold-rolled steel, or galvanized steel, featuring a thickness typically ranging from 1.5mm to 2mm.
Real case-Main Techinical Parameters
Flow chart
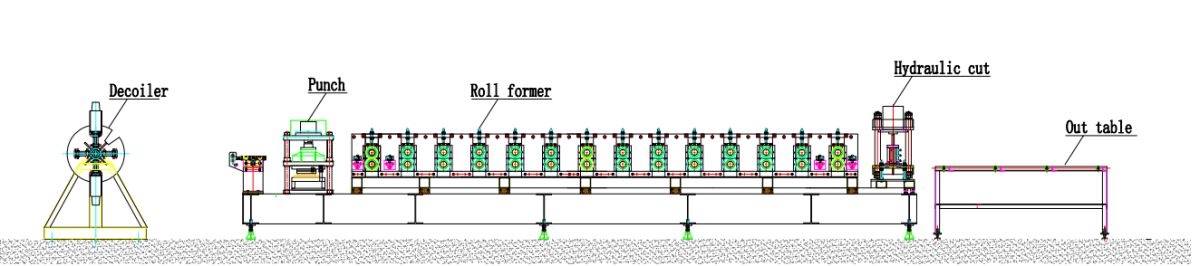
The manual decoiler is equipped with a brake device, allowing for core expansion adjustment between φ490-510 mm, ensuring smooth uncoiling. Moreover, an outward coil retainer prevents coil slippage, boosting cost-effectiveness and safety. In the case of the hydraulic decoiler, a press arm secures the steel coil, mitigating the risk of coil spring-up and potential worker injury. To meet increased production demands, we provide an optional hydraulic decoiler powered by a hydraulic station.
Manual decoiler--Guiding--Hydraulic punch--Roll forming machine--Hydraulic cut--Out table
Main Techinical Parameters
1.Line speed: 0-12m/min without punching, 3m/min with punching.
2.Material thickness: 2mm in this case.
3.Suitable material: Hot rolled steel, cold rolled steel, galvanized steel.
4.Roll forming machine: Wall-panel structure and chain driving system.
5.No. Of forming station: 20
6.Punching system: Hydraulic, roll former stops when punching.
7.Cutting system:Hydraulic, roll former stops when cutting.
8.Changing size:2-3 hours manually.
9.PLC cabinet: Siemens system.
Real case-Description
Manual Decoiler
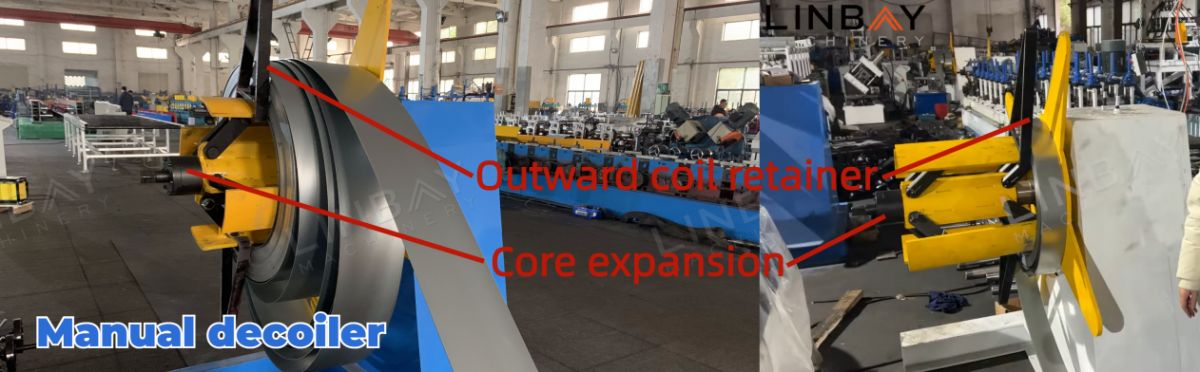
Guiding
Guiding rollers play a crucial role in maintaining alignment between the steel coil and the machine, preventing distortion of the strut channel.
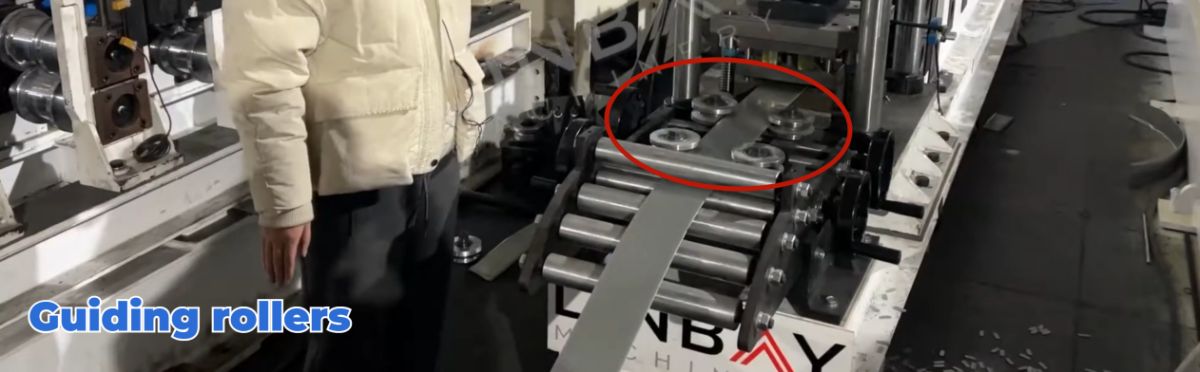
Guiding rollers play a crucial role in the forming process, preventing rebound deformation of the strip steel. The straightness of the tube beam is essential for product quality, impacting the supporting performance of the entire installation frame. Guiding rollers are strategically installed along the entire roll forming machine, not just at the inlet. Before shipment, we measure the distance from each guiding roller to the machine's edge and document these measurements in the manual. In the event of slight displacements during transportation or the production process, workers can use this recorded data to reposition the rollers accurately.
Hydraulic Punch
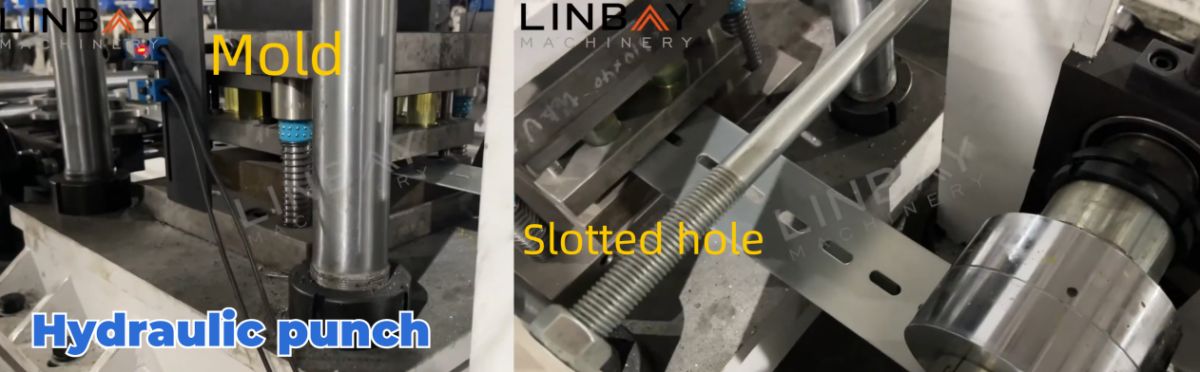
The hydraulic punch, powered by a hydraulic station, is located in front of the roll forming machine, necessitating a pause in the roll forming process during punching. The hydraulic punch machine is configured with a punch step of 400 mm. For increased production speed, we suggest an independent hydraulic punching solution tailored to the provided punching drawings.
Roll Forming Machine
The roll forming machine features a wall panel structure and a chain-driving system, providing a cost-effective solution for manual size changes with a replacement time of about 2-3 hours.
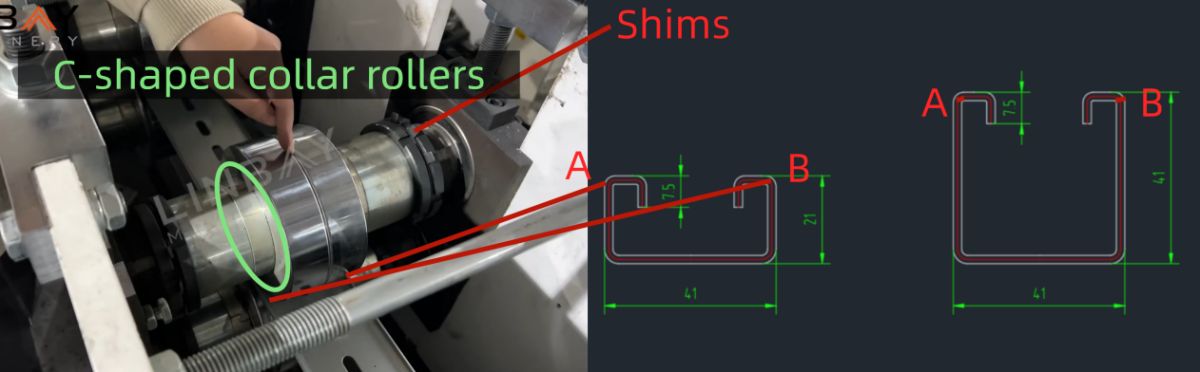
Adjusting the forming points is crucial for changing sizes. Loosening the shims at the ends of the rollers and replacing or adding C-shaped collar rollers (sleeves) at the appropriate position shifts the forming point for the new profile size. Additionally, we provide an automatic size change solution with a replacement time of approximately 10 minutes.
Video link to -【Installation】Linbay Change sleeves for roll forming machine
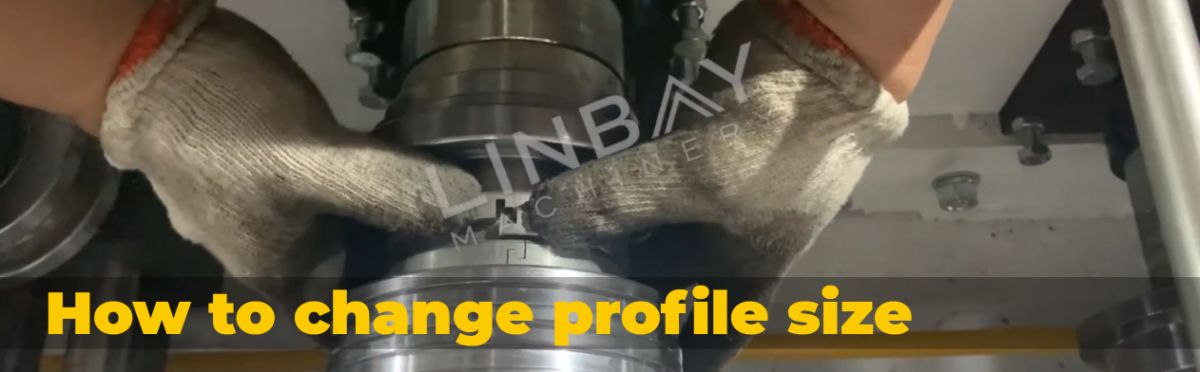
Hydraulic cutting
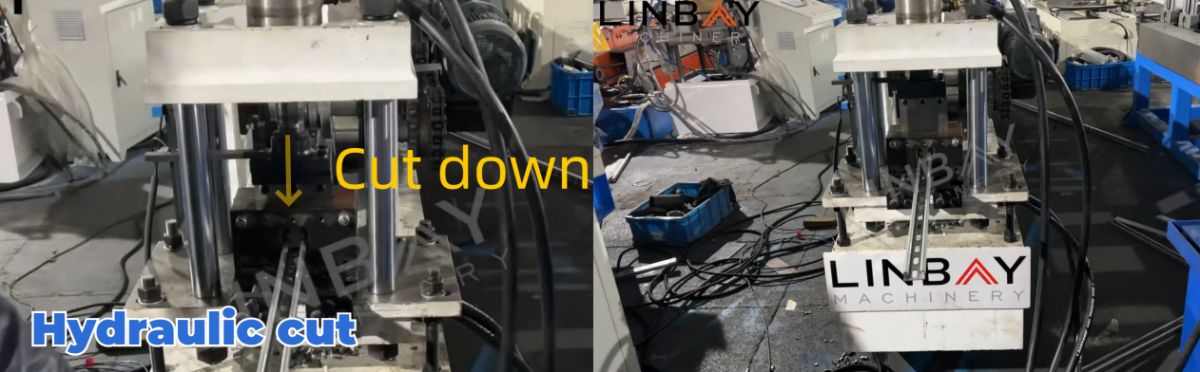
The hydraulic cutting machine, operated by a hydraulic station, is proficient in cutting 2mm thick steel coils. Its cutting blades are tailored to the profile shape, producing around 8mm of waste material per cut while maintaining a nearly burr-free cutting surface.
Encoder & PLC
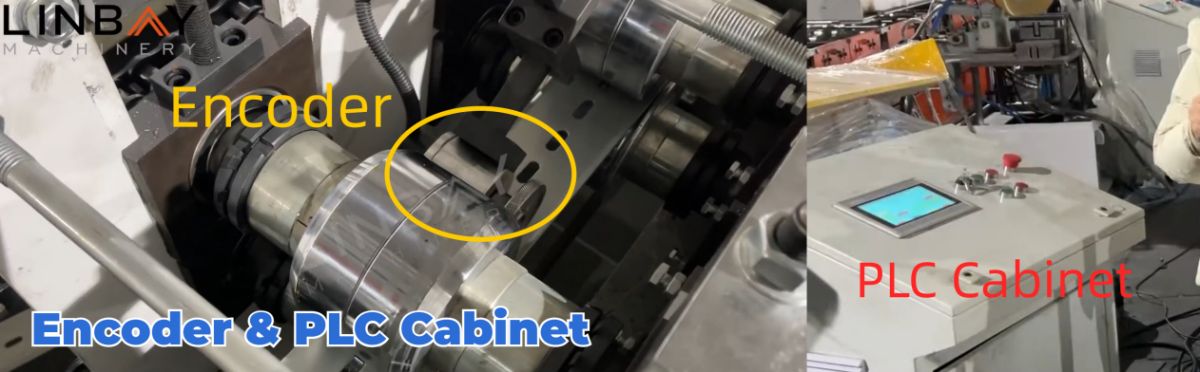
The roll forming machine incorporates a Japanese brand Koyo encoder, which translates sensed coil lengths into electrical signals transmitted to the PLC control cabinet. This precise system ensures that cutting errors are kept within a range of ±1mm, ensuring the production of high-quality products while minimizing waste from incorrect cuts. Operators can conveniently control production speed, production dimensions, cutting length, and more through the PLC screen. Additionally, the PLC control cabinet features memory storage for commonly used parameters and provides protection functions such as overload, short circuit, and phase loss.
The language on the PLC screen can be customized based on customer preferences.
Hydraulic Station
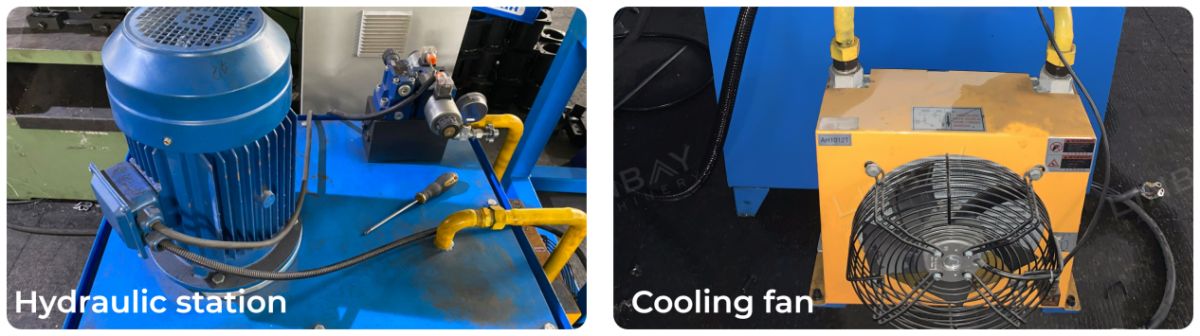
Our hydraulic station is equipped with cooling electric fans to efficiently dissipate heat, ensuring prolonged and reliable operation with a low failure rate, adapting to a hot working environment.
Warranty
On the day of shipment, the current date will be engraved on the metal nameplate, marking the commencement of a two-year guarantee for the entire production line and a five-year warranty for rollers and shafts.
1. Decoiler
2. Feeding
3.Punching
4. Roll forming stands
5. Driving system
6. Cutting system
Others
Out table